What is Curtain Wall Aluminium Veneer System?
Curtain wall aluminium veneer system is a kind of aluminium alloy veneer as the main material of the building envelope, belongs to the non-load-bearing external wall system. It is connected to the main structure of the building through the metal support frame (keel system), and the aluminium veneer is used as the external decorative panel, which is both functional (such as waterproofing, heat preservation, and sound insulation) and decorative (diversified shapes, colours, and surface treatments). Its core features include light weight, strong weather resistance and plasticity, and it is widely used in the facades of commercial buildings, public facilities and high-rise buildings.
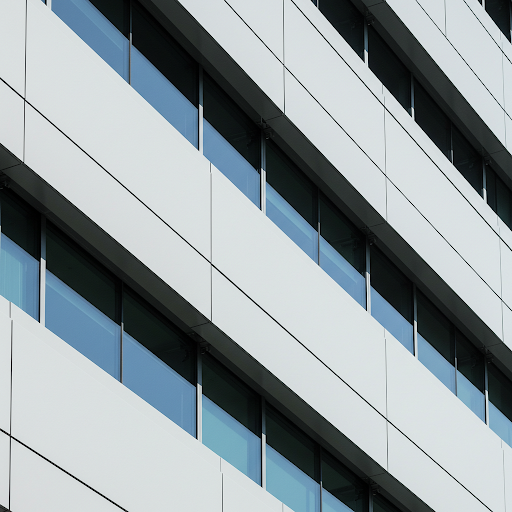
Common Structural Forms
1. Unitised Curtain Wall (Unitary Curtain Wall)
Definition and Characteristics:
Unitised Curtain Wall is a highly industrialized curtain wall system in which all components (aluminium veneer, support frames, seals, insulation, etc.) are prefabricated into independent unit modules (usually one floor height or sub-block) in the factory, and then directly lifted and connected with the building structure after being transported to the site.
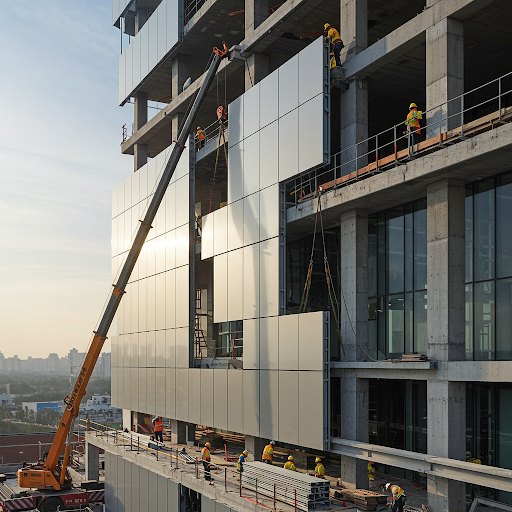
- Modular design ensures high installation precision and fast construction speed, which is suitable for ultra-high-rise or large-scale projects.
Structural Composition:
- Unit module: Integrated by aluminium profile keel, aluminium veneer panel, heat insulation material, sealing adhesive strip, and so on.
- Connection system: Fixed with neighbouring units and the main structure by hanging or plugging, forming a continuous external wall interface.
- Seam treatment: Multi-seal design (adhesive strip + sealant) is adopted to guarantee waterproof and airtightness.
Advantages:
- Efficient construction: Only module lifting is required on site, reducing labour and time costs.
- Controlled quality: Factory prefabrication ensures processing precision and material consistency.
- Strong adaptability: Suitable for complex facade modelling or buildings with high seismic requirements.
Applicable Scenes:
Super-high-rise office buildings, large commercial complexes, airport terminals and other projects with tight schedule or high degree of façade standardisation.
2. Stick System Curtain Wall
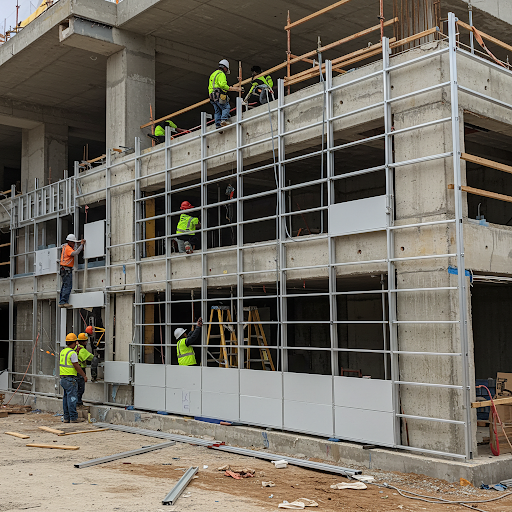
Definition and Characteristics:
Stick System Curtain Wall adopts the mode of ‘on-site assembly’, all the keels (vertical columns, horizontal beams) and aluminium veneer panels are installed on site piece by piece.
- Highly flexible, can be adjusted according to the site conditions, and is suitable for shaped or irregular building facades.
Structural Composition:
- Supporting frame: It consists of vertical aluminium columns (main keel) and horizontal aluminium beams (secondary keel) to form a grid-like skeleton, which is fixed to the building structure through angle yards or bolts.
- Panel fixing: Aluminium veneer is fixed on the keel through angle yards, screws or pressure blocks, and the joints are filled with sealant.
- Functional layer: Thermal insulation cotton, waterproof membrane, etc. are usually filled or laid on site after the skeleton is installed.
Advantages:
- Flexible adaptation: Can cope with complex geometries or later design changes.
- Controllable costs: Low material transport and storage costs, suitable for small and medium-sized projects.
- Convenient maintenance: Single panel can be dismantled and replaced independently, low maintenance cost.
Applicable Scenarios:
Small and medium-sized buildings, shaped buildings (such as curved surfaces, folding line modelling), renovation projects or local curtain wall renewal projects.
System Comparison and Selection
Characteristics | Monolithic Curtain Wall | Modular Curtain Wall |
---|---|---|
Installation Speed | Very fast (modular lifting) | Slower (piece-by-piece installation on site) |
Costs | Higher costs (factory prefabrication + transport) | Lower costs (mainly on-site processing) |
Precision and Quality | High (standardised factory production) | Dependent on site construction level |
Applicable Scale | Large/Ultra-High-Rise Buildings | Small/Medium/Shaped Buildings |
Maintenance Convenience | Complexity of Module Replacement | Convenient Repair of Single Panel |
System Composition
The curtain wall aluminium veneer system consists of a number of core components working together to ensure structural stability, sealing and decorative effect. The following is a detailed description of its composition and function:
1. Aluminium Veneer Panel
Definition and Function:
Aluminium veneer is the outer decorative and protective surface layer of the system, made of aluminium alloy sheet by cutting, bending, welding, surface treatment and other processes.
- Core function: Resist environmental erosion such as wind and rain, ultraviolet rays, provide architectural aesthetic effect, auxiliary heat insulation, sound insulation.
Material and Design Points:
- Material: Commonly used 3003, 5005 series aluminium alloy, the thickness is usually 2.0~5.0mm (outdoor commonly used more than 2.5mm).
- Surface treatment:
- Fluorocarbon spraying (PVDF): Excellent weather resistance, UV resistance, corrosion resistance, suitable for outdoor environment.
- Polyester spraying (PE): Lower cost, suitable for indoor or low corrosion environment.
- Anodising: Strong metallic texture, good abrasion resistance.
- Modelling design: Can be customised with plane, curved surface, punching, hollowing and other shaped structures to meet personalised façade requirements.
- Fixing method: Connected with keel through angle yards, bolts or pressure blocks, need to reserve space for thermal expansion and contraction.
2. Skeleton (Beams, Vertical Columns)
Definition and Function:
Skeleton is the support structure of the system, consisting of vertical columns (main keel) and horizontal beams (secondary keel) to form a grid-like framework, bear the load of aluminium veneer and transfer it to the main body of the building.
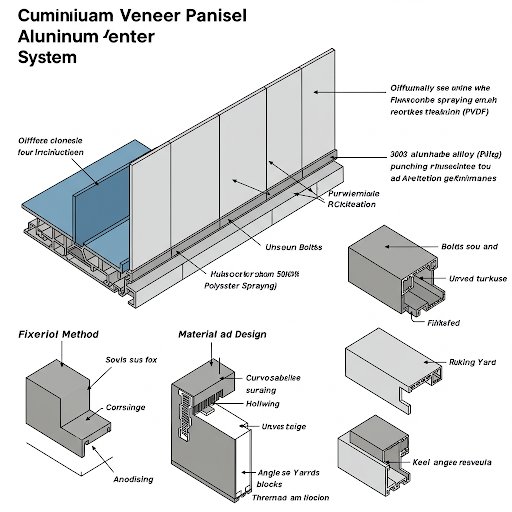
Material and Structure Design:
- Material:
- Aluminium alloy profile: Lightweight, corrosion-resistant, commonly used 6063-T5/T6 series.
- Steel: Used for large-span or ultra-high curtain wall (need to do hot dip galvanised or fluorocarbon spray anti-corrosion treatment).
- Connection method:
- Vertical column: Anchored to the building structure (beams and columns) through angle yards or pre-embedded parts, with adjustable supports to accommodate installation errors.
- Horizontal beams: Connected with vertical columns through bolts or plugs to form a stable grid.
- Layout design:
- Calculate the keel spacing (usually ≤1.2m) according to the aluminium veneer size, wind load, seismic force, etc.
- Reserve expansion joints (about 15~25mm) to cope with temperature deformation.
3. Sealing Materials and Accessories
Definition and Function:
Sealing materials are used to fill the gaps between panels, frames and panels to ensure the waterproof, airtight and soundproof performance of the system.
Main Types and Selection:
- Sealing tape:
- EPDM rubber strip: Aging-resistant, good elasticity, used for sealing joints of unit-type curtain wall.
- Silicone rubber strip: High temperature resistance, strong weather resistance, suitable for complex climatic environment.
- Sealant:
- Silicone weathering adhesive: High elasticity, UV resistance, used for panel joint filling (e.g. Dow Corning DC795).
- Polyurethane adhesive: Strong bonding, suitable for keel and panel joints.
- Other accessories:
- Drainage channel: Water guide hidden in the joints to prevent rainwater infiltration.
- Foam stick: Fill the bottom of the joints, control the thickness of sealant, avoid bonding on three sides.
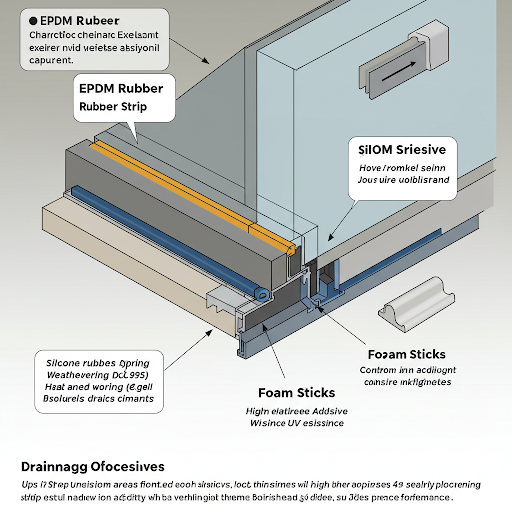
Construction Points:
- Seam cleaning: Remove dust and oil before glue injection to ensure bonding strength.
- Multiple sealing: Adopt the double protection design of ‘adhesive strip + sealant’ to enhance the waterproof performance.
4. Connectors and Mounting Brackets
Definition and Function:
Connectors are the ‘bridge’ between the curtain wall system and the main body of the building, ensuring the safe transfer of loads and allowing a slight displacement to release stress.
Type and Design:
- Angle yards:
- L-shaped aluminium or stainless steel parts for fixing vertical columns to the building structure.
- Pre-embedded or fixed by chemical anchors/expansion bolts, adjustable in three dimensions (±20mm).
- Hook-up system:
- Specialised for unitary curtain walls, for quick lifting of modules by means of hooks or slots.
- Adapter:
- Used to adjust the distance between the keel and the main structure (e.g. steel adapter to solve the problem of large overhangs).
- Lightning protection connectors:
- Connect the curtain wall frame with the building lightning protection system, made of stainless steel or galvanised steel.
Material and Anti-corrosion Requirements:
- Stainless steel (304/316): High corrosion resistance, for use in wet or coastal environments.
- Hot-dipped galvanised steel: Lower cost, periodic checking of coating integrity required.
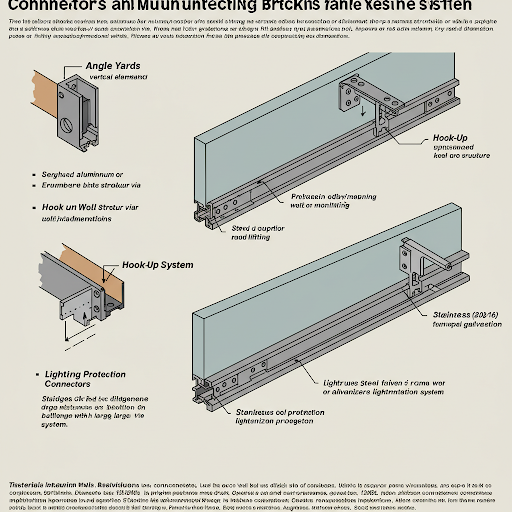
System Components Synergy Points
- Compensation for thermal expansion and contraction: Expansion joints are reserved between the aluminium veneer and the keel to avoid deformation due to temperature stress.
- Equal pressure cavity design: Set up a cavity inside the joints to balance the internal and external air pressure and prevent rainwater infiltration.
- Fireproof isolation: Fireproof rock wool or galvanised steel plates are set between layers to block the spread of fire.
Customisation Options
Customisation Dimensions | Examples of Optional Contents | Description |
---|---|---|
Alloy Material | 3003, 5052, 5005, etc. | Strength and corrosion resistance vary slightly between alloys. |
Surface Finishes | PE/PVDF sprayed; powder coated; woodgrain transfer | Weather resistance, decorative effect and cost are all important. |
Plate thickness | 1.0-3.0mm (can be customised) | Thickness affects strength, weight and cost. |
Moulding process | Punching, bending, carving, shaped cutting | Complicated process increases processing time and cost. |
Module size | Standard plate; oversized plate; shaped plate | Large size or shaped requires special lifting and transport. |
Design and Manufacturing Process
The design and manufacture of curtain wall aluminium veneer systems needs to follow a standardised process to ensure quality control throughout the entire cycle from concept to implementation. The following is a detailed description of the core process:
1. Demand Communication and Technical Negotiation
Objective:
To clarify customer requirements, building conditions and technical specifications, and lay the foundation for design.
Key Steps:
- Demand collection:
- Building use, façade effect (colour, shape, slit design).
- Performance requirements: Wind pressure resistance level (e.g. ≥3kPa), waterproof level, heat insulation and sound insulation index.
- Site survey:
- Measurement of the deviation of the main building structure, review of the position of pre-embedded parts.
- Analysis of environmental factors: Local wind load, seismic intensity, temperature and humidity changes.
- Technical confirmation:
- Material selection (aluminium thickness, coating type, keel specification).
- Connection method (unit type/component type), fire and lightning protection design.
2. Programme Design and Rendering (Revit, CAD)
Goal:
Transform the requirements into a visualisation scheme to guide the subsequent production and construction.
Process & Tools:
- 3D modelling:
- Use Revit, Rhino and other software to establish a BIM model of the building facade, optimise the logic of aluminium panel segmentation and splicing.
- Simulate the structural stress, thermal performance and drainage path.
- Construction drawing deepening:
- CAD drawing keel layout, node sample drawing (such as corner, edge processing).
- Marking processing size, tolerance (±1mm), installation holes.
- Rendering:
- Generate realistic renderings through 3ds Max or Lumion for customers to confirm the colour and shape.
3. Sample Production and Confirmation
Goal:
Verify the feasibility of design and ensure the consistency of mass production.
Key Link:
- Sample production:
- Process 1:1 partial aluminium plate (including surface treatment) according to design drawings, assemble skeleton connecting nodes.
- Performance test:
- Coating test: Colour difference test (ΔE≤1.5), adhesion (scratch method ≥4B), salt spray resistance (≥3000 hours).
- Structure test: Simulated wind pressure, water tightness (spray test).
- Customer Confirmation:
- Sign to confirm the sample effect, lock the technical parameters and acceptance criteria.
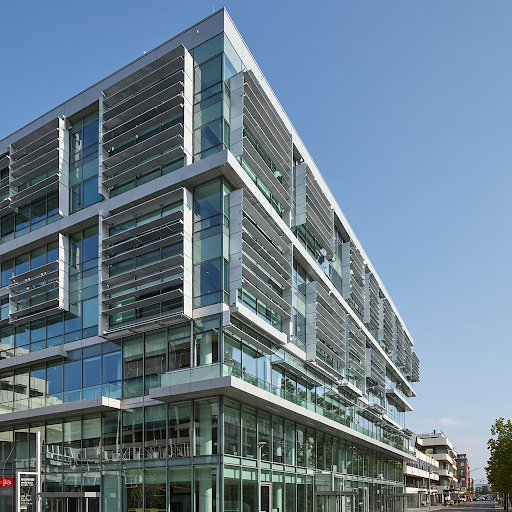
4. Batch Processing (CNC cutting, bending, spraying/painting)
Objective:
To complete the production of aluminium veneer and supporting components efficiently and accurately.
Process Flow:
- Aluminium panel pre-processing:
- Sheet uncoiling → CNC cutting (laser/turret punch) → bending and forming (precision ±0.5mm).
- Welding and grinding:
- Reinforcement welding (argon arc welding) → welding point polishing to ensure surface flatness (Ra≤0.1mm).
- Surface treatment:
- Spraying line process:
- Degreasing → chroming treatment → primer → fluorocarbon topcoat (two coats and one baking/three coats and two baking) → curing (230℃ baking).
- Anodic oxidation: Electrolytic colouring → sealing hole treatment, film thickness ≥15μm.
- Spraying line process:
- Accessories processing:
- Cutting and drilling of keel profile → welding of adapter → anti-corrosion treatment (e.g. sandblasting + fluorocarbon spraying).
5. Quality Inspection and Packaging Shipment
Goal:
Ensure that 100% of the ex-factory products comply with the technical specifications.
Inspection Items:
- Appearance inspection:
- No surface scratches, colour difference, coating bubbles, bending angle error ≤1°.
- Size sampling inspection:
- Diagonal deviation ≤2mm, hole offset ≤1mm (according to GB/T 23443-2009 standard).
- Performance sampling:
- Randomly take samples for simulated load test, sealant peeling strength test.
Packaging and Transport:
- Loss-proof packaging:
- Aluminium plate covered with protective film → pearl cotton wrapped → wooden box fixed (spacing ≤ 800mm).
- Logistic marking:
- Mark ‘up’, ‘fragile’ and batch number to avoid stacking and collision.
6. On-site Installation Guidance and Acceptance
Objective:
To ensure the construction quality and design effect.
Key Steps:
- Technical briefing:
- Provide the installation manual to the constructor to clarify the keel positioning, panel fixing sequence and sealant application process.
- Process guidance:
- Supervise the verticality of keel (deviation ≤3mm/2m) and the width of adhesive seam (6~12mm).
- Instruct unit-type curtain wall lifting alignment (error ≤2mm).
- Completion and acceptance:
- Functionality test: Drenching test (no leakage for 15 minutes), airtightness test.
- Appearance acceptance: Overall flatness (≤2mm/2m), glue seam straightness (≤1mm).
- Submission of completion information: Warranty, test report, hidden works records.
Process Optimisation Points
- Digital management: Adopt ERP/MES system to track the production progress and reduce human error.
- Flexible production: Reserve 5% margin to cope with design change or patch demand.
- Collaborative work: Design and construction teams work together in real time to quickly solve on-site problems (e.g. hole deviation).
Advantages and Application Scenarios
With its unique advantages, the curtain wall aluminium veneer system is widely used in modern buildings, which can meet aesthetic demands and guarantee functionality and durability. The following is a detailed analysis of its core advantages and typical application scenarios:
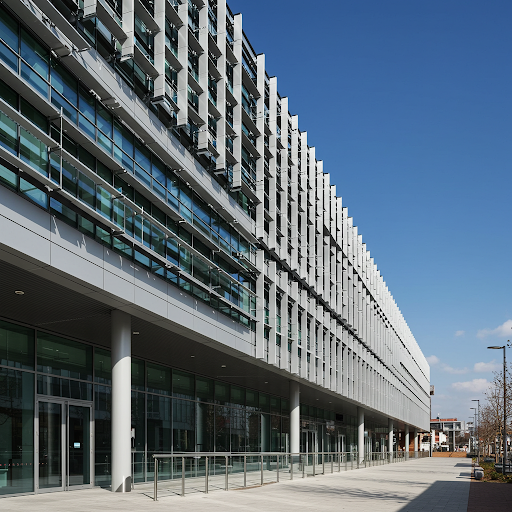
1. Highly Personalised: To Meet the Designer’s Creativity and the Owner’s Brand Image
Core Advantages:
- Free modelling:
- Aluminium veneer can be CNC bending, punching, engraving and other processes to achieve plane, curved, wavy, hollow and other complex shapes, suitable for shaped buildings (such as hyperbolic dome, spiral façade).
- Support customised slit design (wide slit, narrow slit, staggered slit) to enhance the rhythm of the façade.
- Various colours and textures:
- Surface treatment: Fluorocarbon spraying (over 200 RAL colours are available), wood grain transfer, stone-like pattern, mirror polishing, etc., to match the architectural style and brand VI (e.g. corporate logo colour).
- Special effects: Gradient colours, brushed metal, anodised matt texture.
- Flexible size:
- The size of veneer can reach 1500mm×4000mm, reducing the number of seams and enhancing the overall sense.
Application Value:
- Brand display: Commercial complexes can strengthen brand recognition through custom patterns or iconic colours.
- Cultural expression: Public buildings (e.g. museums, theatres) use relief or openwork design to convey regional cultural elements.
2. Performance Advantage: Functionality and Durability at the Same Time
Core Performance:
- Fire safety:
- Aluminium plate is class A non-combustible material (GB8624-2012) with a melting point of 660°C. Combined with fireproof rock wool filling, it meets the fire code for high-rise buildings.
- Weatherproof and anti-corrosion:
- Fluorocarbon coating is UV-resistant (no obvious fading for 25 years) and acid rain-resistant (no corrosion in pH3~11 environment), which is suitable for coastal or industrial polluted areas.
- Anodic oxide film hardness ≥13μm, wear resistance is better than ordinary coatings.
- Easy to clean and maintain:
- The surface is smooth and hydrophobic, and rainwater can remove dust, reducing cleaning costs (e.g. high altitude façade of airport terminal building).
- Lightweight & Strength:
- Density 2.7g/cm³ (only 1/3 of stone), tensile strength ≥150MPa, reducing building loads.
- Technical Certification:
- Comply with GB/T 23443-2009 aluminium veneer for building decoration standard, and pass ASTM B117 salt spray test (≥3000 hours).
3. Application Fields: Suitable for Diversified Architectural Scenes
表格
复制
Scene Type | Application Characteristics | Typical Cases |
---|---|---|
Commercial complexes | Large-area curtain wall + personalised modelling to attract passenger flow; LED backlit perforated panels for dynamic advertising display. | Shanghai Worldport, Beijing SKP |
Office building | Simple line design to enhance business image; high reflectivity mirror surface aluminium plate to reduce light pollution. | Shenzhen Ping An Finance Centre, Guangzhou Chow Tai Fook Finance Centre |
Airport/Transportation Hub | Weather-resistant + self-cleaning, adaptable to complex climate; curved shape optimises aerodynamics. | Beijing Daxing Airport, Dubai International Airport |
Hotels and Exhibition Centres | Metallic texture + lighting combination creates a sense of luxury; oversized panels reduce seams and enhance integrity. | Atlantis Sanya Hotel, China National Convention Centre II |
Public Facilities | Vandalism-resistant and easy to maintain; openwork design for light and shade. | Library, gymnasium, metro station |
Synergy Advantages and Summary
- Economical: Low life-cycle maintenance costs (no need for frequent renovations) despite high initial costs.
- Sustainability: Aluminium is 100% recyclable, reducing construction waste and meeting green building certifications (LEED, BREEAM).
- Rapid response: Digital design + modular production, shortening the project cycle (saving 30% of the construction period compared to stone curtain wall).